Working with the OPEVA project, funded under the EU CHIPS Act, we are advancing the innovation in developing wireless battery-free sensing solutions for the next generation of EVs. With the development of passive RFID sensor tags, we are utilizing UHF RFID wireless technology to enable SoH monitoring of EV battery cells. To make the wireless communication inside the metallic-caged battery packs in EVs, we analyzed the complete battery environment through electromagnetic simulation tools.
As electric vehicles (EVs) continue to revolutionize the automotive industry, the demand for efficient and reliable battery management systems (BMS) has grown significantly. Traditional BMS, reliant on physical connectors and complex wiring, often faces challenges such as added weight, increased costs, and limited scalability. Enter the wireless battery management system (wBMS)—a groundbreaking innovation designed to address these limitations. By eliminating physical connections and integrating battery-free wireless sensors, wBMS not only enhances system reliability and flexibility but also paves the way for lighter, more cost-effective EV designs. This blog explores the potential of wBMS and the transformative role of battery-free wireless sensors in shaping the future of electric mobility.
Introduction to wireless BMS (wBMS) and battery-free wireless sensors
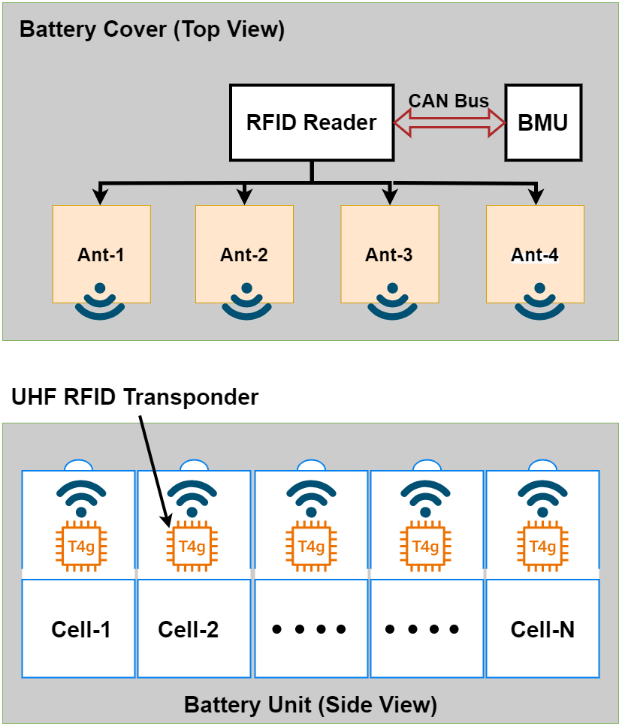
Figure 1: general architecture of Wireless RFID sensing solution for EV wBMS
Electromagnetic Field Analysis of Wireless Communications within the Battery Pack
The electromagnetic field (EMF) analysis of wireless communications within EV battery packs faces challenges like electromagnetic interference (EMI) from the dense metallic environment and external sources, multipath propagation causing signal degradation, and limited frequency band performance. High temperatures, compact designs, and the need for real-time, reliable data transfer further complicate communication. Additionally, regulatory compliance, cost considerations, and maintaining energy efficiency add to the complexity of developing robust wireless solutions. Extensive simulations analysis help us understand how tag-reader communication within the battery pack performs.
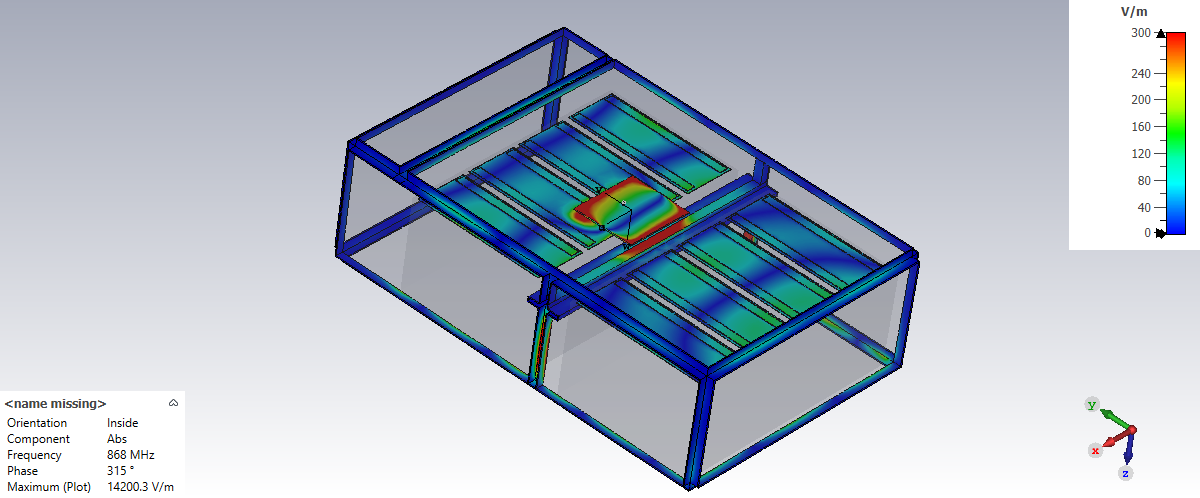
Figure 2: Electromagnetic simulation and analysis of full EV battery pack (Flash Battery).
Advancements in experimental testing of wireless Temperature RFID sensors within the battery pack
UniPG has made significant strides in developing wireless temperature sensing solutions using commercially off-the-shelf (COTS) components, such as the EM4325 chip by EM Microelectronics and the Magnus S3 chip by RF Micron. These high-sensitivity chips were utilized for RAIN RFID applications, with the EM4325 supporting both passive and semi-passive configurations, while the Magnus S3 specialized in environmental sensing, including temperature.
Key achievements of the project include:
- multi-sensor passive tag data acquisition, covering temperature and strain measurements.
- Design, fabrication, and testing of custom metal-mountable tags for metallic battery environments, with performance validated through EM simulations.
- Passive temperature sensing using Magnus S3 and EM4325 chips.
- Development of a software application for data acquisition, visualization, and recording via the ThingMagic m6e Nano RFID reader.
The culmination of this effort was the successful live demonstration (Demo-3) during the General Review Meeting in Perugia, showcasing wireless temperature sensing in a mock battery setup. This breakthrough highlights the potential of passive and semi-passive sensing technologies in advanced industrial applications.
RFID Reader to BMS integration (FLBT)
The RFID reader will send different triggers to different tags placed on each cell group, and read the result in terms of temperature and other transmitted quantities (e.g., strain). The data will then be sent via CANBUS to the battery pack master board. The BMS will process the data and output it to the real-time monitor.
Challenges and future research direction
During the design of our battery-free, wireless strain and temperature sensing system for EV battery management, we encountered numerous challenges, including ensuring reliable operation in harsh metallic environments, maintaining chip-antenna impedance matching under dynamic conditions, achieving passive operation without external power sources, and accurately measuring both strain and temperature. To address these, we developed a custom metal-mountable RFID tag antenna optimized for metallic environments and integrated the Magnus®-S3 chip, utilizing its self-tuning Chameleon™ engine to dynamically adjust impedance and maintain performance. Separating strain and temperature effects, a critical challenge for real-world applications, was resolved through advanced modeling techniques like polynomial fitting to precisely correlate capacitance and sensor responses. For temperature sensing, we overcame issues of environmental interference and signal noise by leveraging the Magnus S3’s environmental sensing capabilities and conducting rigorous electromagnetic simulations to validate accuracy. The final system was extensively tested and optimized for seamless integration with battery management systems, demonstrating a robust, scalable, and energy-efficient solution for next-generation EVs.
Future research in battery-free, wireless strain and temperature sensing systems for EV battery management can focus on enhancing sensor sensitivity and accuracy in extreme environments, such as higher temperature ranges and more confined metallic setups. Advanced materials, such as piezoelectric or nanocomposite-based sensing elements, could be explored to improve durability and responsiveness under prolonged mechanical and thermal stress. Integrating machine learning algorithms with RFID data could enable predictive analytics for strain and temperature patterns, further optimizing battery performance and extending lifespan. Additionally, expanding the sensing system to monitor other critical parameters, such as pressure and humidity, would provide a comprehensive solution for EV battery health monitoring. Efforts should also be directed toward reducing the system’s size and cost for large-scale deployment while maintaining high reliability.